Przemysł stoczniowy w Polsce: rozmowa z Prezesem Cezarym Koseskim z firmy MARKOS [część 1]
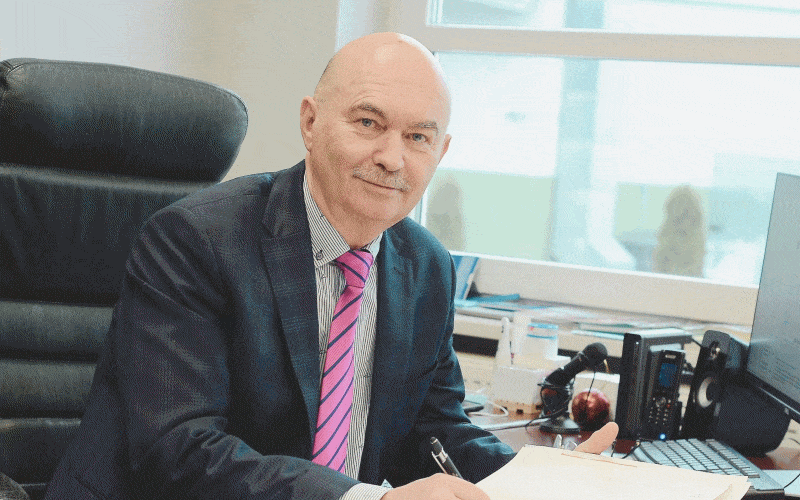
O potencjale firmy MARKOS, budowie łodzi na rynki zachodnie oraz przyszłych zamówieniach rozmawiał z wydawcą Portalu Stoczniowego Mariuszem Dasiewiczem Prezes Cezary Koseski. Firma MARKOS to jeden z czołowych producentów łodzi budowanych z kompozytów w Polsce i Europie Środkowej.
Podczas pierwszej części naszej rozmowy z Prezesem Cezarym Koseskim omówimy kluczowe kwestie branży stoczniowej, w tym rolę kompozytów i technologie offshore. Prezes Koseski podzielił się również tym, co przyciąga do firmy MARKOS zarówno klientów, jak i pracowników, oraz jak przedsiębiorstwo radzi sobie z aktualnymi wyzwaniami. W dyskusji poruszono również temat przyszłości przemysłu stoczniowego w Polsce i na świecie oraz plany firmy w obliczu zbliżających się zmian w branży.
Mariusz Dasiewicz: Czy mógłby Pan podzielić się swoimi spostrzeżeniami dotyczącymi ewolucji i znaczenia kompozytów w budowie łodzi, a także opisać ich przewagę jako materiału używanego do ich konstrukcji?
Cezary Koseski: Pamiętam moje początki w tej branży, kiedy kształtowałem się pod okiem wytrawnych specjalistów. Wówczas, odwiedzając Mazury, przeważała liczba łodzi zbudowanych z drewna i sklejki. Te wykonane z laminatu były rzadkością i wzbudzały duże zainteresowanie.
Rozważając ewolucję kompozytów, warto spojrzeć na ich drogę rozwoju, zwłaszcza w kontekście łodzi produkowanych przez naszą firmę MARKOS.
Kompozyty nie stanowią nowości w branży. Wspomnę tylko, że pierwsze przepisy Polskiego Rejestru Statków dotyczące konstrukcji łodzi laminatowych datują się na rok 1960. Zachowaliśmy te regulacje w naszej firmie. Ich objętość była niewielka – miały format małego przewodnika A5. Od czasu do czasu przeglądamy je z zainteresowaniem, zastanawiając się nad ich prostotą i zwięzłością. Zostały one sporządzone przez ekspertów z Politechniki Gdańskiej we współpracy z kadrą Stoczni Marynarki Wojennej tamtych czasów.
Jeśli chodzi o historię zastosowania laminatów w Polsce, moja wiedza wskazuje na Stocznię Marynarki Wojennej jako punkt początkowy. W latach 50. XX wieku wybudowano tam halę przeznaczoną do konstruowania dużych laminatowych kadłubów dla niszczycieli min. Kluczową rolę odgrywał niski magnetyzm laminatów. W ramach tych działań uruchomiono produkcję różnych komponentów. Firma Krosglass zaczęła dostarczać wówczas nowatorskie tkaniny i maty szklane. Z kolei zakłady w Sarzynie rozpoczęły produkcję żywic poliestrowych, spełniając potrzeby produkcji jednostek. Były to działania na skalę eksperymentalną.
Po wybudowaniu kilku kadłubów w Stoczni Marynarki Wojennej, zdecydowano o przeniesieniu produkcji do stoczni w Ustce. To właśnie tamta stocznia stała się wiodącym producentem laminatowych kompozytów w Polsce, stosowanych głównie w konstrukcji jednostek pływających. Przez lata intensywnie rozwijano tam technologię kompozytów.
W latach 70. XX wieku, podczas moich studiów na Politechnice Gdańskiej, miałem już okazję uczestniczyć w zajęciach dotyczących kompozytów. Wspominam moje początki i pierwsze prace pod okiem doświadczonych naukowców. Kiedy w tamtym okresie odwiedzałem Mazury, dominowały łodzie budowane z drewna lub sklejki. Łodzie z laminatu były rzadkością, stanowiąc prawdziwe cacka dla znawców.
Sytuacja zaczęła się dynamicznie zmieniać, kiedy producenci masowo wprowadzili do produkcji jednostki pływające wykonane z laminatu. Owe materiały wyróżniają się nie tylko swoimi właściwościami, ale także możliwością szybkiego i kosztowo efektywnego przetwarzania w porównaniu z drewnianymi konstrukcjami. Laminat oferuje szybkość i powtarzalność w produkcji, co stanowi jego główną zaletę w kontekście budowy łodzi.
Po dynamicznym rozwoju w zakresie prostych laminatów poliestrowo-szklanych, Polska przeszła do kolejnej fazy ewolucji: wprowadzenia kompozytów, które znalazły zastosowanie również w innych sektorach i stały się kluczowe dla ich postępu. Dziś ciężko wyobrazić sobie dziedzinę, w której kompozyty nie są używane: od przemysłu lotniczego, przez sporty wyczynowe, aż po Formułę 1 – w każdym z tych obszarów materiały kompozytowe odgrywają fundamentalną rolę.
W przeszłości poszycia samolotów, wykonane głównie z stopów aluminium, zastąpione zostały dzisiaj przez kompozyty. Podobna sytuacja ma miejsce w dziedzinie sportów wyczynowych, gdzie niemal wszędzie dominują materiały kompozytowe. W przypadku wyścigów samochodowych, jak Formuła 1, znaczący odsetek elementów osłonowych wykonany jest z wytrzymałych kompozytów.
Jedną z najważniejszych zalet kompozytów w stosunku do metali jest ich wytrzymałość. Odpowiednio dobrana mieszanka składników pozwala osiągnąć wytrzymałość porównywalną, a czasami nawet wyższą niż w przypadku metali. Innym kluczowym atutem jest wysoki moduł sprężystości materiału kompozytowego. Kompozyty są zdolne do pochłaniania dużej ilości energii podczas uderzenia i powrotu do pierwotnej formy, co odróżnia je od metali, które się trwale odkształcają.
Czytaj więcej: https://portalstoczniowy.pl/drony-jako-grozba-dla-infrastruktury-krytycznej-wywiad/
Kompozyty, choć charakteryzują się wieloma zaletami, często bywają pomijane w dyskusjach dotyczących polskiego przemysłu stoczniowego. Ich właściwości, takie jak lekkość, wytrzymałość czy odporność na korozję, a także możliwość adaptacji do specyficznych potrzeb, czynią je doskonałym materiałem w produkcji łodzi.
Ich znaczenie w budowie łodzi jest nie do przecenienia z kilku istotnych powodów takich jak:
· Przede wszystkim, dzięki ich lekkości i wytrzymałości, łodzie wykonane z kompozytów cechują się lepszymi parametrami użytkowymi. Lekkość tych łodzi przyczynia się do redukcji zużycia paliwa, zapewniając jednocześnie wyższą prędkość oraz zasięg.
· Łodzie wykonane z kompozytów charakteryzują się większą odpornością na korozję w porównaniu do wielu tradycyjnych materiałów stoczniowych. Oznacza to, że są one bardziej trwałe i potrzebują mniej konserwacji.
· Kompozyty umożliwiają producentom większą elastyczność w projektowaniu i formowaniu kształtów łodzi, co pozwala na bardziej precyzyjne dopasowanie jednostek do indywidualnych wymagań użytkowników.
Cieszy mnie, że podjęliśmy tę dyskusję. Jestem przekonany, że polski przemysł stoczniowy mógłby znacząco skorzystać na wykorzystaniu kompozytów. Kluczem do tego jest edukacja – musimy skuteczniej edukować naszych inżynierów i producentów o korzyściach płynących z zastosowania kompozytów, aby w pełni rozwinąć potencjał tych innowacyjnych materiałów.
M.D. Jakie unikalne cechy lub wartości, Pana zdaniem, wyróżniają waszą firmę na tle innych pracodawców w branży stoczniowej? Co przyciąga do MARKOS pracowników i klientów?
C.K.: Choć działamy w sektorze stoczniowym, nie jesteśmy typową firmą tego segmentu rynku. Co nas wyróżnia? Przede wszystkim szeroki zakres naszej działalności – dostarczamy produkty dla rozmaitych branż. Balansujemy między obszarem energetyki wiatrowej a segmentem budowy łodzi, zarówno tych przeznaczonych dla przemysłu okrętowego, jak i dla turystyki. Nie zapominając także o sektorze motoryzacyjnym. Obecność MARKOS w tak wielu obszarach sprawia, że nie jesteśmy jedynie firmą stoczniową, ale raczej wszechstronnym dostawcą rozwiązań dla różnorodnych sektorów.
Owa różnorodność okazała się naszym atutem, szczególnie w trudnych czasach. Gdy w latach 2008-2009 przemysł jachtowy doświadczał spadków, nasza zróżnicowana oferta pozwoliła nam zrównoważyć straty. Nasza zdolność do adaptacji i elastyczności ekonomicznej sprawia, że potrafimy kończyć każdy rok z pozytywnym wynikiem. Dzięki temu możemy łagodzić efekty spowolnień w jednym sektorze, korzystając z możliwości w innych. To właśnie ta elastyczność jest naszą największą przewagą na rynku.
Wyróżniamy się na tle konkurencji, podejmując się trudnych wyzwań z determinacją. Nasza współpraca ze Stocznią Marynarki Wojennej przy budowie Ślązaka udowodniła, że nawet skomplikowane tematy nie są dla nas przeszkodą. To buduje zaufanie wśród klientów, którzy często zgłaszają się do nas z własnej inicjatywy. Współpracujemy nie tylko z partnerami z Niemiec, ale także z innych części Europy. Dobrym tego przykładem jest współpraca z firmą ze Szwajcarii, dla której realizujemy specjalistyczne projekty. Bez względu na poziom trudności, zawsze potrafimy sprostać oczekiwaniom klientów. Uważam, że nasza zdolność do radzenia sobie z wyzwaniami wynika z wielobranżowego doświadczenia naszych technologów, którzy nie skupiają się tylko na jednym obszarze, ale czerpią wiedzę z różnych dziedzin.
Kluczem do naszego sukcesu jest też inwestowanie w rozwój pracowników. Od lat prowadzimy dział szkoleniowy skierowany dla kadry produkcyjnej. Wielu z naszych nowych pracowników, zwłaszcza tych zajmujących się kompozytami, zaczyna pracę bez wcześniejszego doświadczenia w tej specjalności. Jako że w Polsce brakuje placówek kształcących w tym zawodzie, każdy nowy pracownik przechodzi u nas gruntowne szkolenie. Dysponujemy zespołem doświadczonych instruktorów, których celem jest efektywne przygotowanie nowych osób do pracy z kompozytami. Wsparcie ze strony bardziej doświadczonych kolegów, którzy są za to odpowiednio wynagradzani, dodatkowo przyspiesza ten proces.
Rozwój pracowników w naszej firmie jest ściśle powiązany z wynagrodzeniem. Za każdy przyswojony etap edukacji, kończący się egzaminem, pracownicy otrzymują podwyżkę lub awansują. Taka finansowa motywacja skłania ich do stałego doskonalenia umiejętności. Jako dowód na efektywność takiego podejścia służą nam pozytywne wyniki audytów przeprowadzanych przez firmy takie jak General Electric czy Siemens oraz regularne kontrole związane z budową jednostek morskich przez Lloyd’s Register. Otrzymane rekomendacje świadczą o wysokim poziomie kwalifikacji naszej kadry.
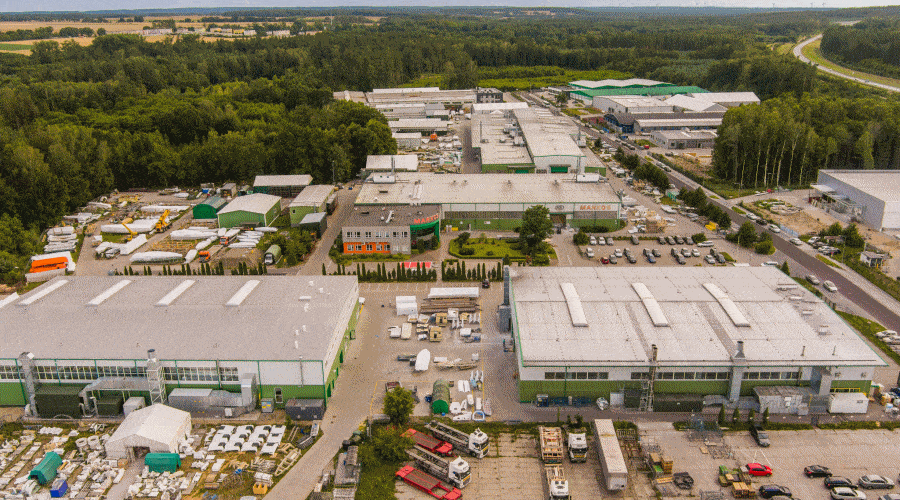
Branża kompozytów wymaga kształcenia pracowników „od podstaw”, ponieważ nie istnieją specjalistyczne szkoły czy kierunki dedykowane tej dziedzinie.
Współpracujemy z różnymi placówkami edukacyjnymi z naszej okolicy. Jako przykład można podać stałą współpracę ze szkołą o profilu mechanicznym. Uczniowie z różnych kierunków, np. ślusarze czy mechanicy, uczestniczą w naszych warsztatach i zdobywają wiedzę z zakresu laminatów. Otrzymują od nas certyfikaty, potwierdzające przeszkolenie w zakresie formowania laminatów. Wielu z nich, po odkryciu pasji do tej branży, dołącza do naszego zespołu jako pełnoprawni specjaliści, mimo braku formalnego wykształcenia w tej dziedzinie.
Czytaj więcej: https://portalstoczniowy.pl/prezes-pgz-stoczni-wojennej-pawel-lulewicz-o-strategii-opartej-na-trzech-filarach-wywiad/
Ostatnio zawarliśmy umowę z jednym z ośrodków edukacyjnych dotyczącą utworzenia klasy kształcącej w zawodzie „monter łodzi i jachtów”. Program szkoleniowy obejmuje kompleksowe zagadnienia – począwszy od podstaw pracy z kompozytami, aż po finalny montaż jednostek. Dzięki temu uczniowie będą mieli możliwość poznania całego procesu produkcyjnego, od pierwszego etapu do gotowego produktu.
Kluczową częścią kształcenia uczniów będzie zgłębianie wiedzy na temat kompozytów, ich właściwości i zastosowań technologicznych. Pokażemy im, jak wytwarzać te materiały, zarówno poprzez teoretyczne lekcje, jak i praktyczne zajęcia w naszym zakładzie.
Aktywnie współdziałamy także z placówkami o innym profilu, na przykład z szkołami o kierunku elektrycznym. W tym roku zakończyliśmy pierwszy rok takiej współpracy. Grupa uczniów z szkoły branżowej regularnie uczestniczyła w praktykach w naszej firmie, poznając praktyczne aspekty instalacji elektrycznych oraz inne kwestie kluczowe dla budowy łodzi i jachtów. Przez trzy dni w tygodniu uczestniczyli w zajęciach, w trakcie których pracowali ramię w ramię z naszymi specjalistami od elektrotechniki. Nasze zakłady są wyposażone w stacje transformatorowe, liczne rozdzielnice oraz zaawansowane urządzenia elektryczne wspierające różnorodne procesy produkcyjne – od prostych odkurzaczy po zaawansowane maszyny technologiczne. Uczniowie mieli okazję brać udział nie tylko w procesach produkcyjnych, ale także w pracach związanych z utrzymaniem i serwisem sprzętu elektrotechnicznego.
Uczniowie mieli okazję zgłębić wiedzę na temat szerokiego spektrum potrzeb związanych z elektrotechniką. Liczymy na to, że w przyszłości staną się integralną częścią naszych zespołów specjalistycznych. W bieżącym roku kontynuują naukę w klasie drugiej, a my z niecierpliwością wyczekujemy kolejnej grupy uczniów. Wzmacnianie kwalifikacji elektryków będzie trwałym składnikiem naszej strategii edukacyjnej, zwłaszcza z uwagi na rosnące zapotrzebowanie na te kompetencje.
Współczesne łodzie i jachty są tak zaawansowane technologicznie, że rosnące zapotrzebowanie na specjalistów od instalacji elektrycznych przewyższa potrzeby związane z mechaniką. Kompleksowość tych instalacji stale się zwiększa. Dodatkowo, podobnie jak w sektorze motoryzacyjnym, obserwujemy boom na rynku napędów elektrycznych. W naszym przedsiębiorstwie, MARKOS, od pewnego czasu skupiamy się na budowie łodzi z takimi napędami, co stanowi nowy wymiar wyzwań dla naszej kadry elektrycznej. Kompleksowe systemy związane z napędem, akumulatory czy sterowanie silnikami elektrycznymi to obszary, w których intensywnie współdziałamy z ośrodkami edukacyjnymi.
Kolejnym priorytetowym działem w MARKOS jest obróbka numeryczna. Aktualnie zatrudniamy ponad dwudziestu operatorów, obsługujących maszyny CNC oraz kilku programistów odpowiedzialnych za tworzenie nowych aplikacji. Dział ten będzie się rozwijał, dlatego nawiązanie i utrzymanie relacji z szkołami kształcącymi w tym kierunku to dla nas priorytet. Wciąż intensyfikujemy współpracę z edukacyjnymi placówkami specjalizującymi się w obróbce numerycznej.
M.D. Czy do pracy na stanowiska, które aktualnie oferuje MARKOS, wymagane są konkretne kwalifikacje czy certyfikaty? Czy te kompetencje są kluczowe do skutecznego funkcjonowania w branży stoczniowej?
C.K.: Nasz zespół składa się z ekspertów wielu specjalności. Pierwszą kategorią są inżynierowie z różnych dziedzin pokrewnych. Część z nich ma wykształcenie w dziedzinie inżynierii materiałowej, w tym również z zakresu chemii. W trakcie studiów zdobywali podstawową wiedzę o kompozytach. Sam fakt posiadania dyplomu świadczy o zdolnościach adaptacyjnych oraz umiejętności uczenia się, co pozwala im szybko wdrożyć się w kwestie kompozytowe. Takie osoby, mając solidne podstawy, mogą w krótkim czasie nabyć specjalistyczne umiejętności, stając się cennym wsparciem dla naszej firmy. Systematycznie rekrutujemy takich specjalistów, którzy świetnie wpisują się w naszą kulturę organizacyjną.
Kolejną grupą są inżynierowie bezpośrednio skoncentrowani na konstrukcji jednostek pływających, takich jak łodzie czy jachty. Osoby z takim wykształceniem kształci m.in. Politechnika Gdańska. Ponieważ realizujemy autorskie projekty, zdobyte tam umiejętności doskonale odnajdują się w praktyce naszej firmy.
Odrębną kategorię stanowią specjaliści związani z obróbką numeryczną, zajmujący się projektowaniem, nadzorowaniem prac i wyborem odpowiednich narzędzi. Jest to zaawansowana wiedza, którą można przyswoić podczas studiów i następnie efektywnie zaadaptować do specyfiki naszej działalności.
Nieustannie poszukujemy talentów w tych kluczowych obszarach, przy czym nie każdy kandydat idealnie wpisuje się w nasze potrzeby. Dodatkowo, część naszego zespołu skupia się na relacjach z klientami. Posiadamy specjalistów, takich jak project managerowie, którzy dzięki znajomości technologii oraz naszej oferty, odpowiadają za utrzymanie relacji i zawieranie kontraktów z kluczowymi klientami. Dzięki dedykowanym zespołom jesteśmy w stanie dostosować naszą ofertę do różnorodnych sektorów rynku, czy to w motoryzacji, czy w branży stoczniowej specjalizującej się w budowie łodzi i jachtów. Do tej grupy regularnie dołączają osoby z wykształceniem inżynierskim, które mają możliwość rozwoju i dalszego kształcenia w zakresie zarządzania projektami.
M.D. W jaki sposób firma MARKOS odnosi się do kwestii zrównoważonego rozwoju i ekologii, mając na uwadze specyfikę przemysłu stoczniowego? Jakie konkretne działania są podejmowane w tej materii?
C.K.: W MARKOS traktujemy zagadnienie zrównoważonego rozwoju i ekologii z pełnym zaangażowaniem, zwłaszcza biorąc pod uwagę, że specyfika naszej działalności wiąże się z przetwarzaniem materiałów chemicznych. Jesteśmy świadomi, że działalność przemysłowa, niezależnie od branży, wpływa na otaczające nas środowisko. Dlatego dokładamy wszelkich starań, by ten wpływ był jak najmniej inwazyjny.
Czytaj więcej: https://portalstoczniowy.pl/dla-portalu-stoczniowego-czlonek-zarzadu-stoczni-crist-jacek-milewski-wywiad/
Chciałbym tutaj wspomnieć o dwóch nowoczesnych halach, które oddaliśmy do użytku w ostatnim czasie. Są one przeznaczone bezpośrednio do przetwarzania kompozytów. W trakcie projektowania i budowy tych obiektów zwróciliśmy szczególną uwagę na spełnienie surowych norm dotyczących emisji szkodliwych substancji. W ramach tych działań, hale zostały wyposażone w zaawansowane systemy wentylacyjne, których głównym zadaniem jest redukcja Styrenu – gazu ulatniającego się podczas pracy z żywicami i wpływającego negatywnie na środowisko. Styren jest organicznym związkiem chemicznym stosowanym między innymi w produkcji polistyrenu oraz różnych żywic i kompozytów. Ulatnia się w postaci gazu i jest jednym z zanieczyszczeń powietrza, które mogą pochodzić z przemysłu przetwarzania tych materiałów. Styren ma specyficzny, intensywny zapach, który jest łatwo rozpoznawalny. Wysokie stężenia tego związku w powietrzu mogą być szkodliwe dla zdrowia i środowiska.
Aby uzyskać pozwolenie na użytkowanie tych hal, musieliśmy dostosować się do standardów gwarantujących bardzo niską emisyjność tych gazów. Wszystkie nasze systemy wentylacyjne są wyposażone w mechanizmy redukujące emisję Styrenu aż do poziomu 90%. Dzięki tym działaniom spełniamy, a często nawet przekraczamy, normy dotyczące ochrony środowiska.
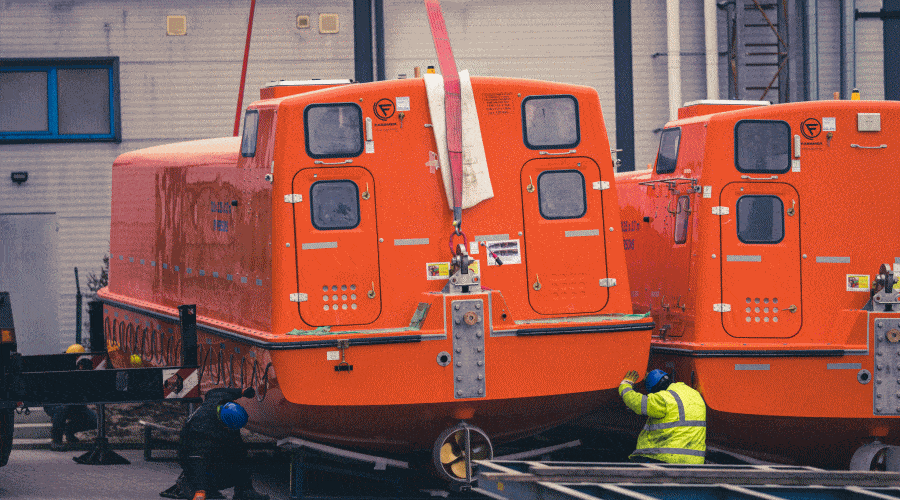
Inne obszary, nad którymi intensywnie pracujemy, dotyczą gospodarki odpadami. Staramy się minimalizować ich ilość poprzez odpowiednie sortowanie oraz poszukiwanie nowych zastosowań. W ramach działalności MARKOS prowadzimy poszukiwania partnerów do współpracy w tym zakresie. Przykładem jest nasza kolaboracja z niemiecką firmą specjalizującą się w recyklingu. Odpady z mat i tkanin szklanych w naszej firmie nie są traktowane jako bezużyteczne, lecz jako surowiec do produkcji nowych materiałów, które mogą być wykorzystane w różnych procesach przemysłowych. To nowatorskie podejście na skalę europejską. Choć jesteśmy na początku tej drogi, współpraca z niemieckim partnerem wydaje się być obiecująca. Naszym celem jest, aby wszystkie elementy mat i tkanin zamiast trafiać do kontenerów na odpady, stały się składnikami procesów produkcyjnych, tworząc materiały o parametrach idealnie dopasowanych do naszej produkcji.
Aktualnie jesteśmy w trakcie przetwarzania pierwszej próbnej partii materiałów, przygotowując je do zastosowania w technikach laminowania, czyli produkcji kompozytów w technologiach zamkniętych. Chodzi tutaj o tzw. technikę RTM (Resin Transfer Molding). Wszystko wskazuje na to, że ten etap zakończy się sukcesem.
Kolejnym krokiem w naszej ekologicznej strategii jest wprowadzenie do produkcji wyłącznie produktów w technologiach zamkniętych, czyli infuzji lub RTM. Tradycyjne technologie, takie jak laminowanie ręczne, polegające na przesycaniu mat i tkanin żywicą, powodowały uwolnienie styrenu do atmosfery, co miało negatywne skutki dla środowiska, nie mówiąc o charakterystycznym, intensywnym zapachu.
Nowoczesne technologie zamknięte, takie jak infuzja czy RTM, skutecznie zablokowały emisję szkodliwych substancji. Te technologie pozwalają na minimalizację emisji, ponieważ cały proces utwardzania zachodzi w układzie zamkniętym – albo pod folią, albo w hermetycznych formach. W porównaniu do starych metod otwartego ręcznego laminowania, które wcześniej były stosowane, obecne technologie znacząco ograniczają wpływ na środowisko.
Aktualnie wszystkie nasze nowatorskie projekty, w tym duże łodzie i jachty motorowe, realizowane są przy użyciu procesów infuzyjnych. Projekty związane z energetyką wiatrową są w całości bazowane na technologiach zamkniętych. W skrócie, dzięki tym rozwiązaniom, redukujemy emisję zarówno w obrębie hali – co poprawia warunki pracy dla naszych pracowników – jak i na zewnątrz, gdzie stosujemy specjalistyczne filtry do zredukowania emisji styrenu.
Podążając w tym kierunku, stawiamy czoła wyzwaniom. Wiele firm z branży energetyki wiatrowej przykłada ogromną wagę do kwestii ekologicznych. Dlatego dostawcy, tacy jak MARKOS, muszą również działać w sposób ekologiczny. Chociaż takie podejście może wiązać się z wyższymi kosztami, jesteśmy kompensowani przez naszych partnerów biznesowych, dla których dbałość o środowisko jest kluczowym elementem misji firmy.
Rozmawiał Mariusz Dasiewicz
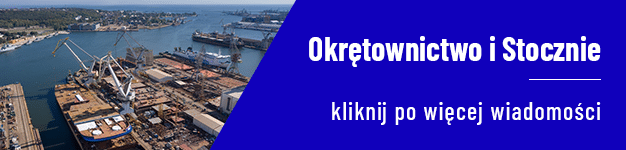
Subskrybuj nasz newsletter!
O nas
Portal Stoczniowy to branżowy serwis informacyjny o przemyśle stoczniowym i marynarkach wojennych, a także innych tematach związanych z szeroko pojętym morzem.
Najpopularniejsze
Portal Stoczniowy 2022 | Wszystkie Prawa Zastrzeżone. Portal Stoczniowy chroni prywatność i dane osobowe swoich pracowników, klientów i kontrahentów. W serwisie wdrożone zostały procedury dotyczące przetwarzania danych osobowych oraz stosowane są jednolite zasady, zapewniające najwyższy stopień ich ochrony.